Tuesday, December 11, 2007
Turn her over and remove the sutures.
A major milestone has been reached by flipping the hull over and begin to remove the copper stitches that are no longer needed.
Carlins
Wednesday, November 28, 2007
Elbow deep in epoxy
Monday, November 26, 2007
Glue
Hanging Knees
Monday, October 22, 2007
Bow, Stern
Is that a boat?
Wow she is really taking shape now. A temporary stick at midship ensures the beam is at spec. Loosely tied off the stern to keep the aft sheer panels in close position. The sheer line takes shape as the panels come together and curve in. For a minute thought about creating a nice solid wood 'wine glass' type stern with some nice gold leaf lettering, but think the rudder would end up hiding it anyway.
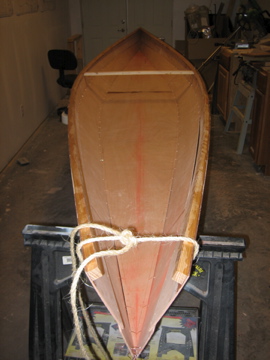
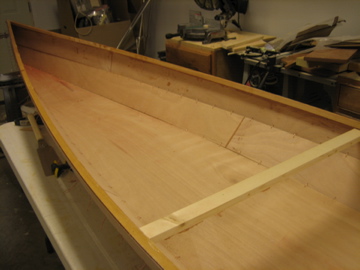
Stitches in detail
Japanese anyone
It was suggested to use a Japanese saw to make all your cuts, never used one before but trusted their judgment. The beauty of the saw apparently is that you push to cut rather than pull as with a more traditional handsaw. This gives you incredible accuracy when cutting bevels, even for a hack like me. Once the bevels were cut, glue, screw and clamp up the joint to produce the bow.
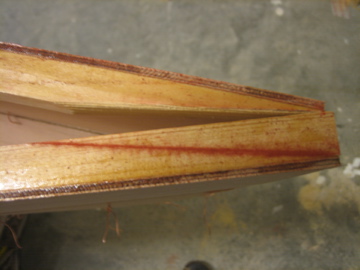
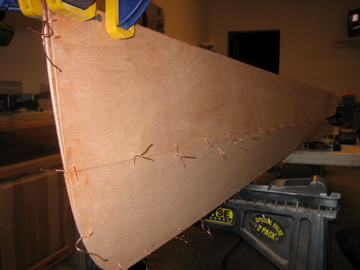
Starboard side
Sheer joy
Time to stitch in the sheer panels. At first this task seemed to be difficult, the instructions left a lot to be figured out on your own, guess thats the fun. Ended up putting a thin piece of plywood across the bilge panels to balance and hold the sheer panels. A clamp allowed to keep it in place for the first few stitches.
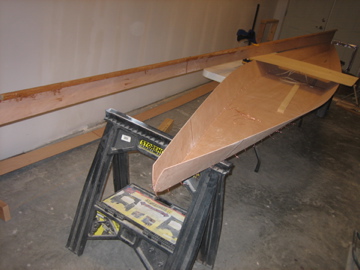
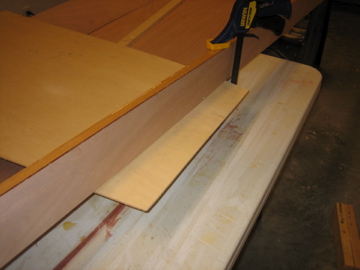
Wednesday, October 17, 2007
Smells like a boat.
In stitches.
Laid out.
Setup the hull/bottom panel on the horses and laid out the bilge panels in prep for stitching. Scribe a pencil line around the bottom panels and drill a hole every 4". Match up the nub on the bilge panels to the bow of the bottom panel and drill a corresponding hole. Start stitching away with copper wire alternating side every 5 or so holes.
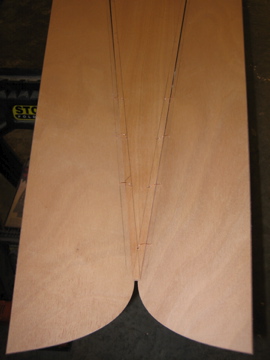
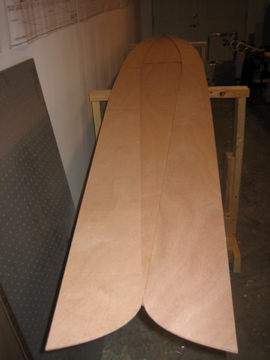
Thursday, October 11, 2007
Nice joints!
The journey begins...
Before gluing up (epoxy + cabosil) the scarfed joints, you protect the wood with clear packing tape and good ole wax paper to avoid a lot of extra sanding when the epoxy squeezes out. Next step is to lay out and tack down the scarfed joints of the sheer, bilge, and hull panels. A straight line ensures proper scarf alignment using set distances at the middle of each scarf.


Bare bones
Preparing for battle
Monday, October 1, 2007
Mill Creek 16.5 (proposed)
Here's a few pics of what I am attempting to build:
Shown here with the optional sailing rig:

Here's a line drawing of the lady:

Here's a write up on the Mill Creek 16.5 (if you are really interested and/or bored)
I've chosen to construct a 'hybrid' version of the Mill Creek, which means the deck will be 'strip built' using cedar strips instead of the mahogony plywood that will be used for the hull and shear. Here's a pic of pattern I will attempt using the strips (minus the American Indian graphic):

Shown here with the optional sailing rig:
Here's a line drawing of the lady:
Here's a write up on the Mill Creek 16.5 (if you are really interested and/or bored)
I've chosen to construct a 'hybrid' version of the Mill Creek, which means the deck will be 'strip built' using cedar strips instead of the mahogony plywood that will be used for the hull and shear. Here's a pic of pattern I will attempt using the strips (minus the American Indian graphic):
Subscribe to:
Posts (Atom)